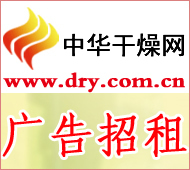
Lithium battery separator is one of the four key materials for lithium batteries. Recently, driven by policy incentives and the lithium battery market, there has been a wave of investment fever in the field of lithium battery separators, with planned production capacity exceeding the global demand. However, due to high technical barriers, the current domestic product yield and quality are not satisfactory, about 80% still need to import. At the 2012 China Lithium Battery Symposium held recently, experts said that under the circumstances that foreign products and technologies continue to maintain competitive advantages, the industry must attach great importance to improving the quality and efficiency of investment, continuously improve the technical system, and establish upstream and downstream integration. Collaboration mechanism, strive to improve the project's productivity and product quality.
Due to the high gross profit margin of diaphragm products and the large market space for import substitution, local governments welcome lithium battery and battery materials projects related to new materials and new energy automotive industries, and usually provide support in terms of land and funds, lithium batteries and their key Materials are favored by the capital market, and the investment boom is surging.
According to data provided by Asian Chemicals Consulting, as of May this year, there are 21 lithium battery separators that have been put into production in China, including Shenzhen Xingyuan Materials, Xinxiang Zhongke Technology, Foshan Jinhui, Nantong Tianfeng, and Tianjin East Membrane Technology Co., Ltd. Etc.; there are 17 membrane production projects under construction and 6 projects in the preparation phase (another batch of unpublished information has not been included in the statistics). Among them, Shenzhen Xingyuan Material Co., Ltd. has achieved the production capacity “continuous jumpâ€: In 2007, it built a 4.8 million square meter/year 16 to 25 μm series of wet process production lines in Dongguan, and sold 3.6 million square meters in the year; January 2008 Launched a high-performance diaphragm production line (dry process) for power lithium batteries with an annual output of 10 million square meters, and started production in September of that year; in November 2010, it invested in a manufacturing base in South China, and will build 13 power lithium battery separator production lines. The project's five production lines (dry process) are expected to be put into operation this year with a production capacity of 60 million square meters. In 2014, the second phase of 7 dry and wet production lines will be completed with a production capacity of 200 million square meters per year. Chongqing Nuomi New Materials Technology Co., Ltd., a company funded and established by Yuntianhua, has established a 15 million square meter/year lithium battery power diaphragm production line in the Changshou Development Zone. It was put into production in October last year.
Industry insiders suggested that if all projects are put into operation on schedule, total domestic production capacity will reach 1.2 billion square meters by 2015, while domestic diaphragm market demand is expected to be only 180 to 240 million square meters, and its output will greatly exceed domestic demand, even Beyond the world's demand.
To the surprise of the industry, the diaphragm production capacity announced in China in 2011 totaled 360 million square meters, while the actual output in the year was only about 40 million square meters, which is only 11% of the total capacity of the year. Why is there such a big gap between the two? The Asian Chemicals Consulting Research believes that the main reason is that it is limited by the production process and technology, and the product yield is low. At present, the lithium battery industry in China has developed rapidly and it has been able to mass produce polypropylene (PP), polyethylene (PE) and other matrix materials. However, these film products, especially high-end separators, are still far from the level of foreign products. Many domestic lithium battery manufacturers prefer to purchase imported diaphragms at high prices in order to ensure the high quality of the products.
Experts emphasized at the seminar that to improve the quality of domestic battery separators as soon as possible, we must accelerate the pace of domestic independent innovation and production-learning-research cooperation, improve product quality and improve production processes, and devote ourselves to the development of high-end products, especially in the manufacture of high-powered diaphragms. Technological breakthrough.
In this regard, some research units and companies have begun to act. For example, inorganic coatings were added to the polymer matrix of Shanghai Silicate at the Chinese Academy of Sciences, which greatly reduced the high-temperature shrinkage of the separator and improved the safety and charge and discharge cycles of lithium-ion batteries. The Institute has cooperated with Hebei Jinli New Energy Materials Technology Company. , to promote industrialization. Shenzhen Huicheng Company developed and produced polyimide (PI) battery separators. Its indirect-controlled subsidiary, Jiangxi Xiancao Nanofiber Technology Co., Ltd.'s PI nanofiber battery separator project, was supported by a national strategic emerging industry fund and a pilot production line. It has been put into operation recently. Yangzi Petrochemical has developed a special polypropylene hydrocarbon material that has been successfully applied to battery separators.
With the development of the new energy automotive industry and the implementation of the goal of reducing the cost of lithium batteries, Asian Chemicals Consulting predicts that the market competition will become more intense in the future. Industry risks mainly come from four aspects. First, the actual speed of pure electric vehicles may not be as expected, leading to a slow trend in the power lithium battery market; second, the international giants promote the continuous upgrading of diaphragm and coating technology, and domestic diaphragms are difficult to enter the high-end market; The domestic diaphragm project production capacity was released centrally, resulting in fierce price competition in the low-end market. Fourth, the international giants expanded their production capacity and may adopt price wars in the low-end market.
To this end, experts have called for the establishment of an upstream, middle, and downstream integrated industrial cooperation mechanism in the rapidly growing domestic lithium battery and separator market. First of all, petrochemical companies should work hard to develop high-quality, low-cost polyolefin-specific materials in accordance with the needs of the diaphragm plant; second, the diaphragm manufacturer maintains close ties with the lithium battery company and aims to improve battery performance and quality; Institutions and universities should aim at the world's advanced level and provide enterprises with timely technical solutions.
There is currently no national standard for lithium battery separators. Experts also suggest that governments or industry associations lead the establishment of third-party membrane testing and trial platforms in China to provide authoritative services for upstream and downstream enterprises and enhance the application of domestic separators by downstream enterprises. Confidence, promote the improvement of the localization rate of the diaphragm.
CIP System,CIP Cleaning System,Juice Automatic CIP Cleaning System,Stainless Steel CIP System
Stainless Steel Tank Co., Ltd. , http://www.worldinstruments.info