China Instrument Network Instrument Development Recently, a new type of chemical nanosensor has been developed at Chalmers University of Technology in Sweden. This technology benefits from the study of atomic layer thickness nanomaterials, which are extremely sensitive to the surrounding environment. .
The sensor is made of a transition metal disulfide. This material interacts strongly with light energy and is considered a new type of sensor material. At the same time, the sensor has an ideal specific surface area when it is made into a thin film. Related research results are published in Nature Communication.
Ermin Malic from Chalmers University said: “Using our method, we can produce fast, efficient, and precise sensors. In the future, this technology can be used to manufacture high-sensitivity and selective sensors in environmental research.â€
The transition metal disulfide has a wide direct band gap, and it easily generates electron-hole bound excitons when irradiated with light, and can be used as an efficient sensor material. These excited "bright" excitons are affected by the surrounding environment, so transition metal disulfides can be used to probe the surrounding environment.
The transition metal disulfide also has a photo-forbidden “dark†excitonic state. The team found that these “dark†excitonic states are converted into “bright†excitons when the molecules are surrounded by dipole moments. A clear additional peak is formed on it.
According to the research team's description, this effect provides an easy-to-recognize optical fingerprint for the probe molecule. This method is much more efficient than traditional detection methods that rely on small changes in the peak position and intensity changes.
The team tested with a typical transition metal disulfide material, tungsten disulfide, and it turned out that the light fingerprinting phenomenon is indeed related to the amount of dipole molecules covered by the sensor material.
With the increase of dipole coverage, the peak corresponding to dark exciton turns into the peak corresponding to the corresponding bright exciton, and the peak position shifts from the high energy side to the low energy side. This effect can be used to directly detect the distribution of dark excitons, and vice versa to detect the distribution of corresponding dipole molecules.
Maja Feierabend of Chalmers University said: “This effect provides new ideas for detecting the air environment. Our method is more effective than traditional sensors that rely on changes in the tiny optical properties.â€
(Original Title: Ultra-thin Nanomaterials Improve Environmental Monitoring Sensitivity)
Plastic Parts Design Services
Compression injection molding: it is an advanced form of traditional injection molding.Advantages: it can increase the flow length ratio of injection molded parts; Adopt less clamping force and injection pressure; Reduce the internal stress of materials; And improve processing productivity.Injection compression molding is applicable to products made of various thermoplastic engineering plastics, such as large-size curved parts, thin-walled parts, miniaturized parts, optical lenses, and parts with good impact resistance requirements.
Low pressure injection molding:Low pressure injection molding process is a packaging process that uses very
low injection pressure to inject hot-melt materials into the mold and solidify rapidly. With the excellent sealing performance and excellent physical and chemical properties of hot-melt materials, it can achieve the effects of insulation, temperature resistance, impact resistance, vibration damping, moisture-proof, waterproof, dustproof and chemical corrosion resistance, and play a good role in protecting electronic components.
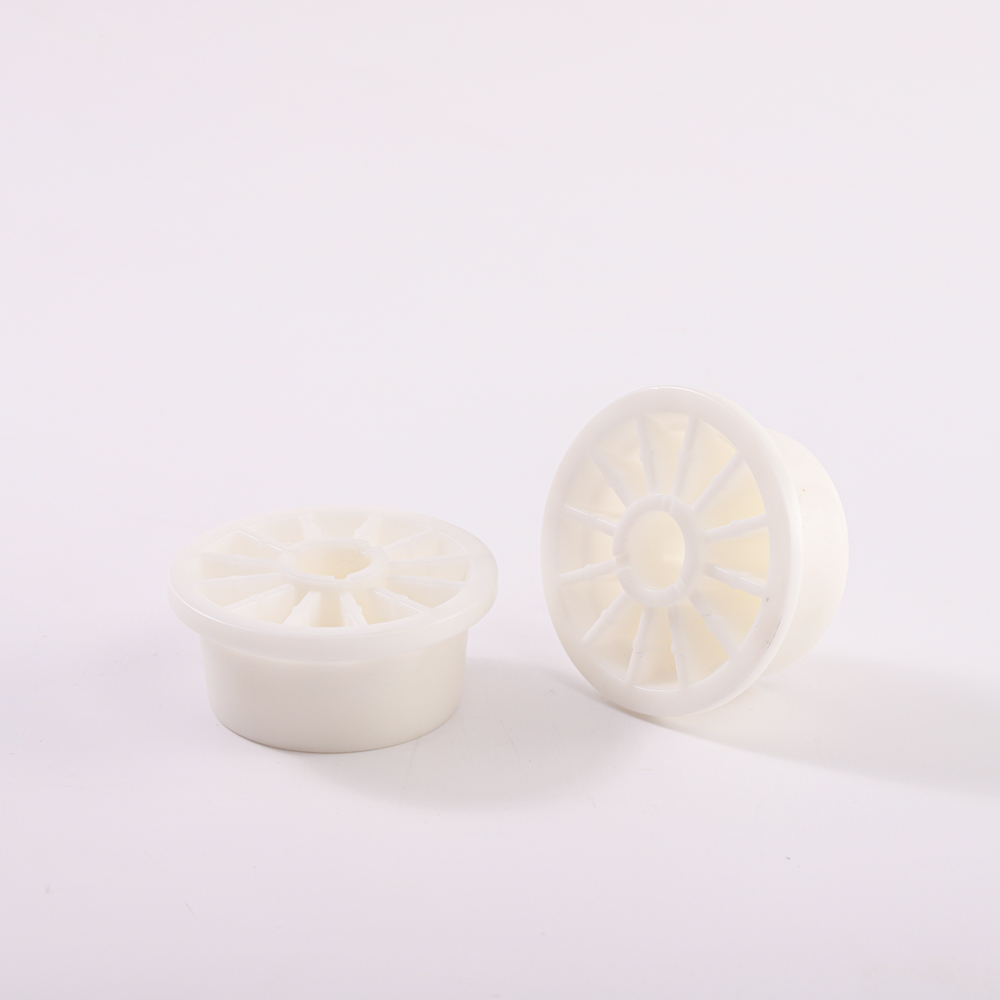
Plastic Parts Design Services,Double Color Plastic Injection Molding Design,Custom Injection Molding Services,Custom-Built Plastic Parts Design Services
Suzhou Dongye Precision Molding Co.,Ltd. , https://www.dongyeinjectionmolding.com