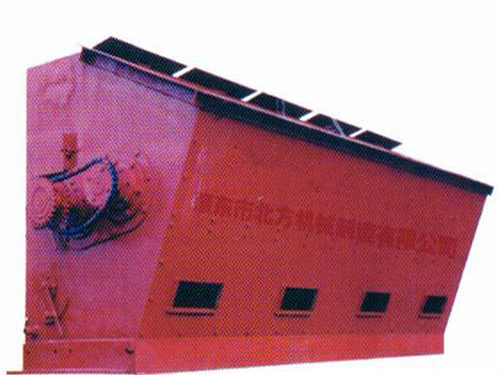
(1) Innovation of coal combustion in stratified branches of coal feeders
Hierarchical branch-type coal-feeding devices are based on the method of stratified coal-supplying, and avoiding short and innovative technologies.
"Layered Branched Coal Feeding Technology" is another way to use poisonous and invade poisonous methods to overcome the shortcomings of local overheat caused by Dulong, and to use its advantages of enhanced combustion and high temperature to break fuel level requirements. In the conventional practice, the coal seam is evenly distributed on the chain row. The single-sided combustion was changed to multi-sided combustion, which increased the burning area of ​​the grate by 30%, orderly disturbance of the fire bed, automatic fire-fighting and continuation of coal, and fierce combustion of the coal seam, which increased the heat load of the grate area and achieved complete combustion with low oxygen uniformity. Achieved a low supply of coal in the market, while increasing the output of thermal storage boilers, thermal efficiency, saving coal, saving electricity and environmental protection; reduce emissions and maintenance. The stratified branch-type coal feeding device arranges the coal into a valley and a ridge peak shape, and a layer of coarse coal is firstly laid on the chain row. To prevent leakage of coal. As the amount of coal moved forward along the chain, the lump coal fell into the valley, and the crushed coal fell on the ridge peak, forming approximately 45 with the ridge heightening process. After the slope, most of the lump coal that fell on the slope also fell to the valley, resulting in secondary stratification. In the valley, the coal seam is thin, with many blocks, and the blast resistance is small. The supply of oxygen is full of fire, and the temperature rise is fast, the fire line is neat, and a uniform fire zone appears on the fire bed. The heat absorption of the radiation surface of the boiler is proportional to the fourth power of the flame temperature, which greatly improves the thermal efficiency. The coal ridge shape formed by the branch (ditch) coal hopper is seen from the process of uniformly burning the fire dragon into pieces, which is the result of the ridged coal creating a free space for intense combustion. When it burns to the front of the grate, it exhibits a thinned flat fire bed, which achieves the goal of even burning and improved combustion efficiency. The degree of complete combustion of the fuel is the precondition and key to the thermal efficiency and output of the boiler. It also directly affects the environmental protection. From the analysis of the characteristics of the combustion zone of coal, it can be seen that the burning rate of coal in the coal seam of the chain layer combustion furnace mainly depends on the gas diffusion rate and is a diffusion combustion zone. In order to increase the degree of complete combustion, it is necessary to enhance the mixing of coal and air and increase the diffusion rate of gas. The combustion of ridge-shaped coal is much more intensified than that of the gates and the flat burning of layered coal. The coal-shaped coal first ignites from the valley, and its volume is continuously shrinking. Together with the turbulence and swirling flow generated by the ridge shape, wind and airflow, and intense burning movement force, the three sides of coal at the ridge peak burn at the same time. (top and both sides), with the combustion process, the ridge peak collapsed, the surface ash flaking off, exposing coal to participate in the combustion. When the fire bed burns to the middle of the combustion chamber, its ridge shape has been transformed into a plane. After air and coal combustion in the combustion process, self-disturbing, mixing and diffusion, etc., after the enhanced combustion, into a flat combustion process, is to break through the plane layer combustion defect process, and combustion is good, and its ash layer will appear Longitudinal longitudinal ridge-shaped vertical transverse corrugation. The ridge-shaped fuel stratification-enhanced combustion mechanism will not change due to different particle sizes of the coal. That is, no matter whether the lump coal is more or more than the end of minced material, it is only necessary to adjust the different air distribution and the minimum and average thickness of the selected coal seam. Compared with the coal seam combustion, the ridge shape is a thin coal seam combustion under the same coal thickness conditions. Because the fire ignited from the gully and burned to the front of the hearth and burned flat, the firebed had been reduced by about 30%. Therefore, it has the characteristics of low oxygen homogenization and intense combustion of thin coal seams, so that the carbon tends to burn completely, which inevitably increases the output and thermal efficiency of the boiler and saves coal and electricity; coal particle size, combustion heat intensity and heat at the valley and ridge peaks Because of the different stresses, the coal-fired rooms are constantly moving relative to each other, so they do not form a large block of coking (covering). In addition, the furnace temperature is high, which broadens the adaptability of the coal. As the grate is evenly heated and the fire bed is not required to be switched on, in addition to achieving uniform and stable combustion, the furnace and maintenance workload and cost are reduced. According to the coal quality, the thickness of the coal seam at the valley, the average and the ridge peak is selected. Under the conditions of reasonable distribution of wind, coal saving efficiency of 6% to 20% can be achieved, and energy saving of 10% to 30% can achieve an ideal energy saving effect.
(2) Transformation method:
According to the actual size of the boiler, a layered branch (ditch) type coal feeder is ordered. After the equipment arrives, the existing furnace hopper is removed and the equipment is installed in place. After adjusting the trial burn, the boiler will enter normal combustion state.
Site construction time (from the removal of the original coal hopper to the completion of installation of new equipment): 3 to 5 days.
Layered coal feeder installations: http://qq8932546.cn.made-in-china.com/
Knits Fabric,Cotton Knit Fabric,Stretch Knit Fabric,Knit Fabric By The Yard
SHAOXING BAOYING TEXTILE CO.,LTD , https://www.baoyingfabric.com